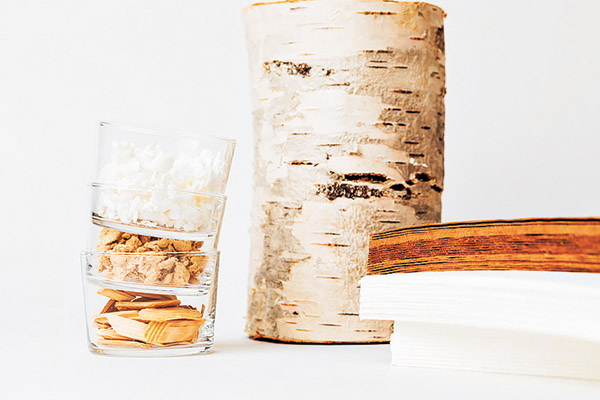
Stora Enso
Industry
Stora Enso
Knock on wood
Stora Enso – the leading provider of renewable solutions in packaging, biomaterials, wood products and paper – believes that everything which is made with fossil-based materials today can be made from a tree tomorrow.
Stora Enso´s global clientele includes the packaging, joinery and construction industries, publishers, retailers, brand owners, print and board producers, printing houses and paper merchants. In 2016, the sales totalled EUR 9.8 billion, and the group has some 25,000 employees in more than 35 countries.
Responding to customer needs and global trends – growing population, urbanization, digitalization, income growth, global warming, changing lifestyles and eco awareness – Stora Enso is developing new climate-friendly alternatives with a smaller carbon footprint. The company sees great innovation potential in fiber-based packaging, high quality paperboards and recyclable products, as well as green solutions in biomaterials. Growing opportunities are seen in the different fractions of biomass from the tree – like cellulose, hemicellulose and lignin.
At the same time Stora Enso is redeveloping ways to reduce weight, costs and environmental impacts of paper and board products.
The laboratory information management system (LIMS) is one tool which Stora Enso uses in the R&D work. Today, two of Stora Enso´s five divisions – Consumer Board and Biomaterials – are using LabVantage Enterprise LIMS provided by Software Point.
New LIMS on board
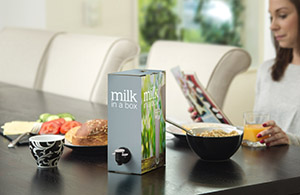
“Because we are a research organization performing both routine analyses and quite demanding tasks, we were not interested in a too simple information system. We wanted a versatile solution and the possibility to adapt it”, Researcher Lena Lindberg recalls.
“However, as we investigated a few alternatives we noticed that the price seemed not to vary so much between different companies. We were not considering a small supplier, but a bigger company to ensure the system is running the next 20 years. A reliable partner. It is very time-consuming and laborious to change the system.”
Lindberg and her internal project group – consisting of eight persons from the research centers in Karlstad, Sweden and in Imatra, Finland – decided to choose LabVantage Enterprise LIMS delivered by Software Point, LabVantage Nordics.
“LabVantage LIMS feels very modern and safe: having a big global company behind it and so many users, the system can´t collapse – it will keep on developing, have new versions, and all the people supporting.”
If we change the way we work, we know that the system can follow us.”
“We discussed with our Software Point team and explained our demands as clearly as possible. Then we did careful documentation: what will be included. When everyone was satisfied with the document, we started the project work and kept regular meetings.”
Between the meetings the Consumer Board project team tested the system. “What was good, what was bad, what was possible to do. We didn´t wish any small installations meanwhile; we wanted the whole LIMS up and running, so we tried to think a bit wider.”
Starting from scratch there are always some challenges. “Many of our prevailing equipment were quite easily connected to the system, but we had slight struggles with certain older devices. Therefore, it was very useful and efficient to have a system specialist from Software Point coming on-site, fixing many small problems in just a couple of days. You must make sure everything is communicating.”
Now looking back to the project era, Lindberg would recommend budgeting more time for the testing periods:
“We had lots of changes done in the meetings, and then 2-3 months in between for testing. If I ever had urgent problems, I could trust there would be help almost immediately. Trust is very important.”
In the beginning of 2016, Consumer Board division launched its new LIMS with 30 regular users in laboratories, mills, among researchers and project leaders.
Web-based value-added
The new LabVantage system has brought many improvements.
“The whole research center uses the same system. If utilizing the storage function, it is possible to see exactly where, in which room, and on which shelf a certain sample is. Moreover, research compilations and the possibility to add attachments – for example a laboratory recipe or a note to a sample – are very useful.”
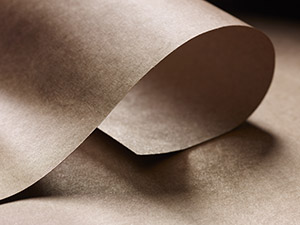
The division has over 100 devices – measuring equipment from basic scales to chromatography and physical properties testing equipment in many locations and connected to the LIMS, so it is very easy to share the results across all the units and regions.
“A huge benefit for an international company is that LabVantage LIMS is web-based. We have people working far away, and now they can see their results directly from China and Brazil. Previously, users had to turn to us asking, for example, to give the figures of last November. Furthermore, it is very practical for people doing remote work.”
“We couldn´t manage without LIMS”, Lena Lindberg sums up.
After all the adventures, Lindberg has no plans of resting on her laurels. The project team has only picked up steam.
“Now that we have come to the base level, we´ll begin developing the system. We want to upgrade to the next version, as there are features we like. Some parts of the electronic laboratory notebook (ELN) could also be very useful for us. I see a lot of improvements in the coming years.”
What a tree can do
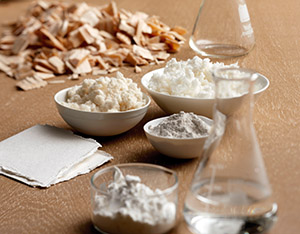
The Innovation Centre for biomaterials unifies research, application, business development and strategic marketing under one roof. The Centre identifies business opportunities in the renewable materials market and links them with leading innovation and research centres in business and academia.
Its new research laboratory facility in Stockholm was inaugurated in December 2015. The Innovation Centre for biomaterials started its LabVantage LIMS project with specification work, and the initial production use started early 2017 with last users planned to join the system after summer 2017.
“Our focus has been more in the Innovation Centre project and strategy work as we have grown our organization, set up new laboratory equipment, hired new people, and worked on our research studies”, Laboratory Manager Linda Renholm describes.
“At the same time, we are implementing the new laboratory information management system all over the organization. As we are still building up our procedures piece by piece, we are not yet using the LIMS with all projects. Everything goes hand in hand.”
The head count of the Innovation Centre for biomaterials is around 70. In addition, the Biomaterials Pulp Competence team in Imatra, Finland, as well as the Danville pilot plant in Virginia, USA and the Raceland demonstration plant in Louisiana, USA are utilizing the new laboratory information management system in their R&D.
“Danville has entered lots of samples in the system with no difficulties. Of course, when launching a new system, it pays the effort to train people how to use the system in the most optimal way. We have also been very satisfied with Software Point´s support. It has been helpful.”
“The biggest benefit of LabVantage Enterprise is the very easy workflow follow-up: what´s happening in the lab, who is to do the work – and I know exactly when the work is finished”, Research Engineer Matti Viikilä exemplifies.
“The increased traceability”, Renholm adds. “It is pretty convenient to see right away from my computer if the chemical I need is already in the building, where, and I can just call the person in charge and ask for it. Also, for some authorities it is necessary to track volumes and report what type of chemicals we have. Overall, we have all data, results and the overview in one system.”
“The LIMS obviously has benefits in analytical routines. Our challenges are merely related to incorporating the system with the R&D world: how to interface and use the features in research and development. We now have LabVantage Enterprise 7, and by updating it to version 8 there may be more features for R&D”, Viikilä sees.
In a truly global company, sharing documentation with a common platform is a big asset in communication.
“Having the same capable system in different parts of Stora Enso increases collaboration, and this is a good thing for the company”, Lena Lindberg concludes.
More info: www.storaenso.com
Text: Software Point
Photos: Stora Enso
24.8.2017