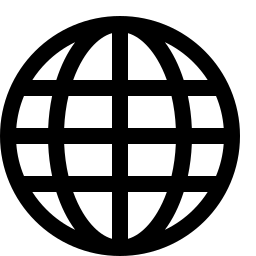
Mercodia
Mercodia
Functionality and fun
How do you go about installing a new laboratory information management system (LIMS) in a biotech company with validated quality system and worldwide clientele? Mercodia´s Bioanalytical Service Coordinator Jenny Tjernberg and Laboratory Service Manager Annika Carlsson report.
Mercodia AB is a Scandinavian biotech company specialized in developing and manufacturing enzyme-linked immunosorbent assays (ELISA) within the area of metabolic disorders. The company´s clientele includes pharmaceutical companies and clinical research organizations around the world.
Exporting over 90 procent of its production from Sweden to 100 countries in all major international markets makes Mercodia the world-leading developer, manufacturer and distributor of high-quality immunoassay kits in the diabetes field.
Mercodia´s ELISA assays can be used in basic, pre-clinical and clinical studies. The company also runs sample analyses for its clients. Samples in the form of serum, plasma or cell culture media are shipped to Mercodia´s main facility in Uppsala, where skilled laboratory technicians analyze them. Each customer receives a custom-made result report adapted to their needs, and the reports can be delivered straight into their system.
To fulfil the needs of the small and large service projects for its customers, Mercodia wanted to replace its previous in-house LIMS with a new and more advanced solution. The company was also looking for additional functionalities like audit trail and quality assurance review.
Mercodia met a number of vendors before choosing Software Point with LabVantage Enterprise LIMS.
“The software seemed to have all the functionality and flexibility we wanted. We also got very good feeling about the company – that we would be able to work together to reach our goal”, Annika Carlsson says.
Finally, Mercodia interviewed two customers already using LabVantage. “They were very happy about the software and the delivery team they had worked with.”
Setting up the project
The project started in February 2016 and was planned to take one year. “We were aware from the start it would require quite an effort to validate and implement such an application”, says Jenny Tjernberg, who worked full-time in the project.
“We hired external resources for project management and validation lead, as we realized this was a competence we lacked internally. The project management combined with the dedicated teams at Mercodia and Software Point, along with the Mercodia board supplying the resources needed for both the project and the improvements of the quality system, is really the success story.”
“The team was great! The product specialists from Software Point and our people worked closely together with daily communication over Slack. They were patient and listened to our thoughts and ideas, but also came up with solutions we could never have found by ourselves.”
However, some surprising events occurred on the way. One thing was the ability to split a sample over two columns when designing a plate in the software. Solving this issue required a major update in the software that came in the new version released in the beginning of 2017.
“We also needed to record who is the technician who runs a certain experiment. We don´t want to log this information manually, as there is a risk to miss it. Together we found an excellent way to catch this information by delivering it with the data file from the plate reader, based on the log in of the operator to the plate reader.”
“Furthermore, we realized that we had gaps in the validation of our computers, servers and IT infra structure. This was a challenge to overcome, but with a happy end and overall improved quality system.”
The original time frame stretched three months into April 2017:
“Setting up the new laboratory information management system required also adapting the company quality system, as there were gaps in how we addressed validation of computerized systems.”
Adaptation of the quality system was a big task, but instead of resistance to change, the Mercodians were curious about the project.
We are a very change-friendly company. The whole company has been dedicated to the project and it will be very beneficial for the future”, emphasizes Carlsson, who is currently planning LIMS-training and celebrations.
Win-win benefits
In Mercodia the LIMS is used by laboratory technicians, managers and quality assurance people who use the system for delivering sample analysis data in good laboratory practice (GLP) and good clinical practice (GCP) studies. The new LIMS brings along a considerable and welcome change in their work practices.
“We realized that the new software can be used for numerous purposes beyond sample analysis. For example, as a library for different kinds of samples we house for assay development projects. This project brought lots of improvement, especially for quality”, Carlsson commends.
“The most important benefits for Mercodia are all the functionalities for performing regulated GLP and GCP studies. No need to transfer data between different systems such as plate reader, excel sheets and complex reports. Calculations of accuracy and precision can be performed within the software. Automated quality assurance review. Less printed papers.”
“To our customers it means improved process for data integrity, and faster turn-over from sample analysis to complete reports.”
Currently Mercodia is setting up an automated system for improved turn-over of sample analysis. “This will shorten the time spent, and increase our resources by reallocating staff to perform more complex parts of our services such as assay development and validation.”
Experience to share
To companies planning a similar project, Jenny Tjernberg and Annika Carlsson would give some advice:
“The project must be prioritized internally, you can´t push lots of other projects at the same time. It is also wise to keep the project group small to be able to make decisions how to move on. Plan well the requirements from the start – what you want of the system – but be ready to adapt different solutions.”
Good project communication is crucial. “You really need a good project manager to manage the communication. We also decided to use Slack as the daily communication tool. Whenever I had a problem or a question, Software Point team answered. We had very friendly and pleasant teamwork together.”
“I think we learned a lot more than we expected, and it has also been more fun than expected!”
More info: www.mercodia.com
Text: Software Point
Photos: Mercodia AB
Caption: Mercodia´s laboratory service team (from the left): Jenny Tjernberg, Annika Carlsson, Sara Hedlund, Fredrik Vellby and Sandra Sköld Chiriac.
22.5.2017